Fortín de Piedra – Soluciones innovadoras en un desarrollo fast track
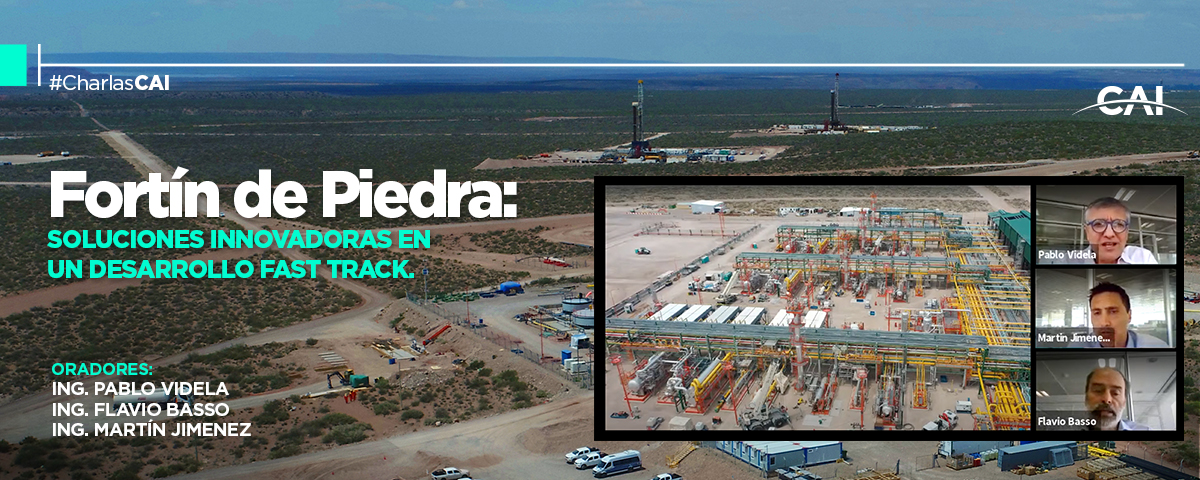
El miércoles 30 de septiembre de 10.30 a 12 horas, a través de la plataforma Zoom, se realizó la #CharlaCAI Fortín de Piedra – Soluciones innovadoras en un desarrollo fast track, cuyos oradores fueron el Ingeniero Pablo Videla, Director Corporativo de Planificación, Control de Gestión y Presupuestos de Techint E&C; el Ingeniero Flavio Basso, Gerente de Suministros de Área Sur, y el Ingeniero Martín Jiménez, Gerente de Proyecto de Fortín de Piedra. Inició la charla el Ingeniero Pablo Videla quien realizó una breve reseña acerca de “las soluciones innovadoras aplicadas en el yacimiento Fortín de Piedra, en Vaca Muerta, Provincia de Neuquén, con el fin de poner en valor el yacimiento”. Videla contó que Tecpetrol fue el desarrollador y Techint E&C construyó el yacimiento y todos los accesorios. “Vaca Muerta es la segunda reserva de gas no convencional del mundo, allí logramos extraer 24 millones de m3 por día, es decir que produce el 13% del gas que se consume en la Argentina, con un diseño que involucró a mil empresas nacionales que contribuyeron a hacerlo posible. Se usaron 7,750 millones horas hombres. Desde que se tomó la decisión de inversión, en marzo de 2017, en seis meses contamos con 6 MM m3 por día. Se instalaron 100 km de ductos y 43 de oleoductos, 22 pads, 4 baterías. Y le pasó a Martín para hablar de las evoluciones de la construcción”, dijo. El Ingeniero Martín Jiménez Álvarez contó que “todos los que integramos estos tres años es un orgullo: La planta central, donde se procesa el gas, sale hacia el gasoducto de exportación y así luego al sistema interconectado. El gas no llega en condiciones de ser comercializado, por eso la planta tiene la misión de quitarle el agua, los hidrocarburos líquidos y demás impurezas con que se extrae el gas. Quisiera comentar que es un Parral: es una vía para centralizar el ruteo donde se ejecutan los diferentes procesos que se utilizan exclusivamente para la transmisión. Son estructuras que están soportadas sobre otras menores que nos permite organizar todo el trabajo de la planta. Carga con muchas horas de mano de obra y de ingeniería, y todo sucede alrededor de los parrales, y es en esos equipos donde se van desarrollando los diferentes procesos. Sin parrales no se interconectan los fluidos, no llegarían los motores, bombas y demás y es por eso que toda nuestra estrategia de construcción se hace pensando en los parrales. En los últimos años las empresas constructoras hemos pensado mucho en bajar los tiempos y los costos en el montaje de los parrales. La modularización de los Parrales lo hacemos íntegramente fuera de la planta y una vez listos, los trasladamos de una sola vez a la planta para instalarlos definitivamente. Estas son cuestiones que se deben decidir al comienzo. Los Parrales tienen una estructura inferior, en la que se generan sendas y caminos para la circulación de personal de la planta, y se le agregan uno o dos niveles de Piping. En el tercero se construye otro por donde corren los cables de electricidad y comunicación. También debe considerarse de forma temprana como se hará el montaje de la estructura de los parrales, lo que nos obliga a diseñarla con refuerzos. Algunas consideraciones: en el inicio que debimos resolver cuáles serían las uniones abulonadas, y cuáles serían las soldadas. Es decir, necesitábamos simplificar los procesos de tendido de cables, la accesibilidad al nivel eléctrico y la mayor cantidad de estructura para poder analizar el costo- beneficio. Finalmente se hace una protección en toda esa estructura como las cuestiones de seguridad, sobre todo. Con esta modularización hemos resuelto este trabajo en solo 3 meses, cuando de la otra forma, la utilizada más comúnmente, hubiéramos tardado 8 meses. Y esto nos ha traído una importante reducción de costos”, explicó. A su turno el Ingeniero Flavio Basso se refirió a todo el proceso de gestión de suministros para el montaje de la planta. Comenzó realizando una enumeración de lo que se debió adquirir a los proveedores: “Válvulas 2559 unidades, Tanques 34 unidades, Bombas 69, Compresores 19, Piping 4500 TN todo realizado por 980 proveedores y 30 subcontratistas. Todo asegurado con la entrega en tiempo y forma. Vamos a mostrar cómo hicimos las compras distribuidas en el mundo: lo importantes es que el 94% se compró en la Argentina, el 4,8% en el resto de américa, un 0,9 en EMEA y 0,1 en Asia”. Para esto se apoyó en un cuadro donde se podía observar la velocidad a la que iba avanzando la gestión de suministros, llegando al 90% en los primeros 6 meses. “Cabe mencionar que a los proveedores no le hemos pedido plazos estándar sino que los plazos debían ser muchísimo menores a los habitual. Los factores principales que nos permitieron comprar de este modo tuvieron que ver con el procedimiento de compra que nos permitiera bajar los ciclos de entrega y la disponibilidad inmediata de los recursos humanos. Y fue clave la compra en Argentina ya que evitamos el tiempo de tránsito y las dificultades aduaneras pero también nos benefició la cercanía del proveedor, y el compromiso de las empresas nacionales con el proyecto. Para todos estos proveedores fue un orgullo trabajar en un proyecto vinculado a Vaca Muerta. En cuanto a la modularización del skids de procesos, nos permitió realizar turnos nocturnos para lograr mayor productividad, menor extensión de la obra civil, mayor control de calidad y más reducción de impacto ambiental, entre otros. En la gestión Post Order, la ventaja fue que teníamos un grupo de inspectores propios para verificar los trabajos y tiempo de los proveedores y realizar inspecciones presenciales, ya que es importante porque se presencia la etapa de verificación y ensayo, algo que permite ganar tiempo. Otra ventaja es el reporte de sistema SAP con el que contamos, ya que permite detectar alertas tempranas. Y finalmente tenemos el tema logístico, en el que hay que seleccionar para la operación de transporte a los vehículos más aptos para poder transportar materiales muy pesados”, relató. Cerca del final, el Ing. Videla retomó la palabra:” Esta es una industria que necesita innovar ya que no lo ha hecho en los últimos 50 años, sin embargo la facturación anual de la industria de la construcción, a nivel global, se estima en 10 billones. Está clasificada por la OIT como una de las industrias de mayor riesgo para los trabajadores; en las últimas décadas la construcción se incrementó en la productividad a razón de 1,90% por año mientras que la economía global avanzó un 2,8 %. En esto existen causas como los factores externos e internos de la industria y además la propia dinámica de la industria. En Techint tenemos una agenda de innovación importante y varios de estos ejes colaboraron en Fortín de Piedra: Mejorar la seguridad y reducir el impacto ambiental, incrementar la competitividad y la previsibilidad y la diferenciación en el producto y en el servicio. Las herramientas que aportamos en este caso son: IMS que es la digitalización e integración de la información; también usamos drones; el Aset Tracking, el monitoreo satelital online que nos permite hacer un mantenimiento predictivo; la realidad virtual modelo 3D, para planificar secuencias de montaje y la credencial BLE, que identifica los tiempos de persona en cada una de las áreas del proyecto”, finalizó.